The Production Part Approval Process (PPAP)
What is The Production Part Approval Process (PPAP)?
The Production Part Approval Process (PPAP) is a standardized process used in the manufacturing industry to ensure that parts and components meet the required quality standards before being mass-produced and delivered to customers. It’s prevalent in the automotive industry but is also used in other sectors where high-quality and reliable production are critical.
Here’s a breakdown of the PPAP process:
PPAP Purpose
The main goal of PPAP is to verify that the supplier’s manufacturing process consistently produces parts that meet all specified requirements. It helps identify potential issues before mass production starts, ensuring that the final product meets the customer’s quality standards.
Levels of PPAP
There are different levels of PPAP, each involving a varying amount of documentation and testing:
- Level 1: Part Submission Warrant (PSW) only.
- Level 2: PSW with Product Samples and Results.
- Level 3: PSW with Product Samples, Results, and Complete Documentation.
- Level 4: PSW with other requirements as specified by the customer.
- Level 5: PSW with Product Samples, Results, and Documentation reviewed at the supplier’s site.
Key Elements of PPAP
The PPAP documentation typically includes several key elements:
- Design Documentation: Includes drawings, specifications, and other design-related documents.
- Engineering Change Documentation: Any changes in the design or manufacturing process. These should be documented and approved.
- Customer-Specific Requirements: Any additional requirements specified by the customer.
- Process Flow Diagram: A diagram that shows the steps in the manufacturing process.
- Process Failure Mode and Effects Analysis (PFMEA): An analysis that identifies potential failure modes in the manufacturing process and their effects.
- Control Plan: A plan that details how the manufacturing process will be controlled to ensure quality.
- Measurement System Analysis (MSA): Analysis of the measurement system to ensure it is accurate and reliable.
- Initial Sample Inspection Report (ISIR): A report showing the results of the initial inspection of the samples.
- Production Part Approval Report (PPAP): A report confirming that the parts meet all the required specifications and are approved for production.
Process Steps
- Submission: The supplier submits the PPAP package to the customer for review.
- Review: The customer reviews the documentation and may request additional information or corrections.
- Approval: Once everything meets the required standards, the customer approves the production part.
- Ongoing Monitoring: Even after approval, ongoing monitoring and audits may be conducted to ensure continued compliance with the requirements.
PPAP Benefits
- Consistency: Ensures parts are produced consistently within the required specifications.
- Risk Reduction: Identifies potential issues before mass production, reducing the risk of defects.
- Customer Confidence: Provides assurance to customers that the supplier can deliver high-quality parts.
Challenges
- Documentation Requirements: The process involves extensive documentation, which can be time-consuming and complex.
- Cost: There may be costs associated with testing and documentation that suppliers need to manage.
Overall, PPAP is a critical process for maintaining high standards in manufacturing and ensuring that products meet both customer and regulatory requirements.
Contact us for an appointment to begin the Nolte Precise Process and discover a total cost solution to your parts fulfillment needs.
“Nolte is in the top 5 of our 75 suppliers, in working with us to make the most of our lean and inventory management
processes.”
Karen K., Supply Chain Manager at Parker-Hannifin’s Oildyne Division (Diversified Manufacturing Company), Minneapolis, MN
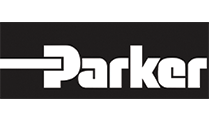