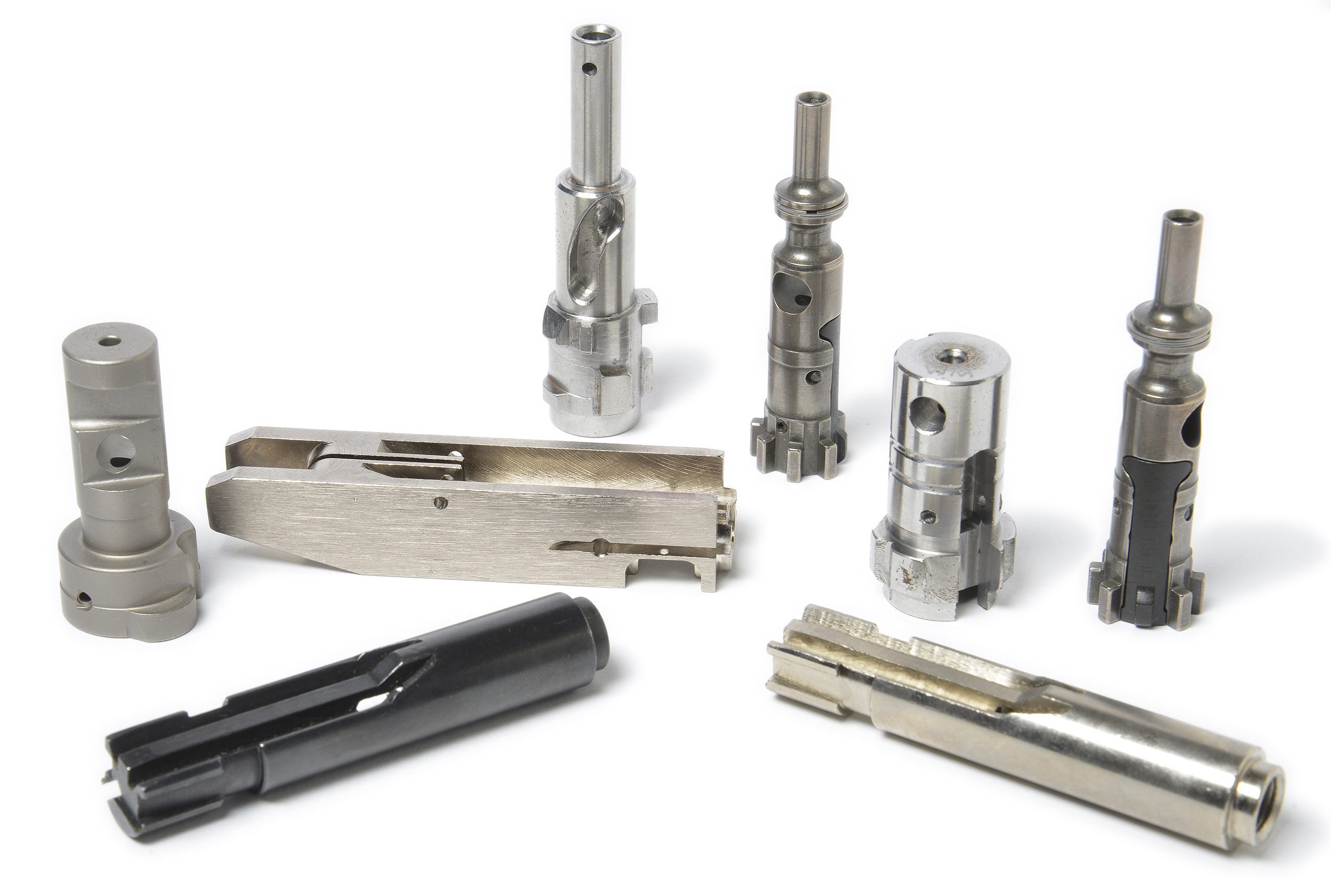
Top 8 tips for designing complex metal parts
When your social media status for your manufactured products is “It’s Complicated”, you know you need a parts manufacturer who can handle the multiple facets of machining complex metal parts. Engineering highly machined parts requires careful consideration of design, material selection, and manufacturability to ensure optimal performance and ease of production. Here are some of the most crucial tips for engineering such parts:
- Design for Manufacturability (DFM)
Design parts with manufacturability in mind. Consider machining capabilities, tool access, and process constraints early in the design phase. Minimize complex geometries and tight tolerances where possible to reduce machining time and costs. Involve machinists and manufacturing engineers early in the design process to leverage their expertise and address potential manufacturability issues. Your machinist can offer the best options for accuracy, tolerances, efficiency, cost-effectiveness and timing.
- Material Selection
Choose suitable materials for the intended application and compatible with machining processes. Consider factors such as machinability, mechanical properties, corrosion resistance, and thermal stability when selecting materials for highly machined parts. Minimize the use of materials that are challenging to machine, such as heat-treated alloys or exotic metals, unless necessary for the application. Avoid features like deep internal pockets, sharp internal corners, or thin walls that may be difficult to machine accurately or lead to tooling issues.
- Optimize Geometry
Design parts with features conducive to machining, such as uniform wall thicknesses, generous fillets, and avoidance of sharp corners or undercuts. Use symmetric designs and standard features to simplify machining setups and reduce the risk of errors.
- Tolerance Analysis
Perform tolerance analysis to establish realistic dimensional and geometric tolerances based on functional requirements and manufacturing capabilities. Use geometric dimensioning and tolerancing (GD&T) to communicate design intent effectively and ensure part interchangeability and assembly compatibility.
- Surface Finishing
Specify surface finish requirements based on functional needs, aesthetics, and manufacturing feasibility. Consider the effects of machining operations on surface finish and plan post-processing treatments if required.
- Consider Part Consolidation
Evaluate opportunities for part consolidation to reduce the number of components and machining operations, simplifying assembly and reducing costs. Combine multiple features into a single part where feasible without compromising functionality or performance.
- Prototype and Test Iteratively
Build prototypes and conduct iterative testing to validate design assumptions, assess manufacturability, and identify opportunities for optimization. Use rapid prototyping techniques or machined prototypes to evaluate fit, form, and function before finalizing the design for production.
- Continuous Improvement
Foster a culture of continuous improvement, where feedback from manufacturing and assembly processes is used to refine future designs and optimize production efficiency. Document lessons learned and best practices for future reference and use in similar projects.
By following these tips, engineers can design highly machined parts that meet performance requirements, are cost-effective to produce, and can be manufactured efficiently with minimal risk of errors or delays. Once you find the right manufacturing partner, make sure to update your product’s social media profile status.
Want to learn more? Contact Nolte Precise Manufacturing to learn more about producing complex metal parts to meet your demanding manufacturing needs.