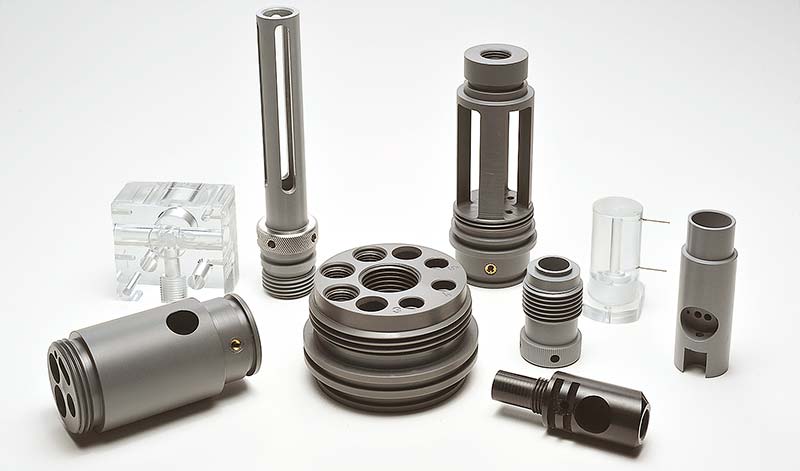
Multi-Step Processes for Manufacturing Complex Metal Parts
If you are afraid of escalators, you should take steps to avoid them. However, manufacturers should never be afraid to incorporate multi-step processing for metal parts. Consider multi-step processing for metal parts under the following conditions:
- Complex Geometry
- Intricate part design: When a part has complex shapes, features, or contours (e.g., pockets, undercuts, tight radii), multi-step processing is essential to achieve the required geometry. Single-step operations often can’t accommodate intricate designs with varied features.
- Multi-axis machining: Parts requiring multiple axes of movement, such as those in 4- or 5-axis CNC machines, often need multiple setups and tool orientations to fully machine all surfaces.
- Tight Tolerances
- High precision: Multi-step machining is necessary when parts require extremely tight tolerances (e.g., +/- 0.001 inch or smaller). After rough cuts, semi-finishing and finishing passes are then applied, focusing on achieving precise dimensions and surface finishes. This layered approach ensures that any slight errors from previous steps are corrected, leading to better overall accuracy.
- Thermal effects: Multi-step processing allows for gradual material removal, which helps manage heat buildup and minimizes thermal expansion that can affect tight tolerances.
- Different Surface Finishes
- Surface finish requirements: Some parts may require varying surface finishes across different areas. Multi-step processing allows for roughing to remove large amounts of material and separate finishing passes to meet specific surface finish requirements (e.g., smoothness, texture).
- Material Properties
- Hard-to-machine materials: Certain materials, such as titanium, Inconel, or hardened steels, may require multiple stages of machining due to their toughness and resistance to cutting. A single-step process may cause excessive tool wear or tool breakage.
- Differing material behavior: Multi-step processes help manage issues like work-hardening or burr formation in materials that require careful handling to maintain part integrity.
- Large Parts or High Material Removal Rates
- Roughing and finishing strategies: When significant material removal is needed, the part typically undergoes a roughing pass to remove bulk material, followed by a finishing pass to achieve final dimensions. This is especially true for large or heavy parts where aggressive roughing could distort the part.
- Tool wear management: Roughing tools are optimized for heavy cuts, while finishing tools are designed for precision. Multi-step processes separate these operations to extend tool life and maintain part quality.
- Consistent quality: Multi-step machining ensures that each part meets specifications for high-volume production runs. Separation of roughing and finishing helps maintain tool integrity and ensures that all parts have consistent surface finish and accuracy. Roughing, semi-finishing, and finishing passes ensure that material removal is controlled, minimizing tool deflection and maintaining dimensional accuracy.
- Efficiency: Multi-step processing may be more efficient in certain cases, such as when large batches can be rough-machined in one phase and then finished in another, optimizing tool wear and cycle time.
- Critical Internal Features
- Internal cavities or channels: When parts have complex internal features like deep pockets, threads, or internal grooves, multi-step processing may be required to access and machine these areas without damaging other features.
- Access limitations: Features like undercuts or internal fillets may require multiple tool setups or special tooling that cannot be completed in a single pass.
- Material Stress and Deformation
- Stress relief: Machining can introduce internal stresses in the material, which may lead to warping or deformation. Multi-step machining processes, including interim stress-relief operations–like heat treatment between steps–can help mitigate these effects and maintain dimensional stability.
- Part stability: For thin-walled or delicate parts, multi-step processing allows gradual material removal to avoid excess vibration, chatter, or deformation during machining.
- High-Value or Critical Parts
- Avoiding scrap: In industries like aerospace or medical device manufacturing where part failure is not acceptable, multi-step processing ensures that parts are inspected and corrected as needed throughout the process, reducing the risk of scrapping expensive materials.
- Process validation: For safety-critical or regulated parts, multi-step machining allows in-process validation and measurement to ensure that quality standards are met at every stage.
- Tooling or Fixturing Limitations
- Multiple setups: If a part requires machining from different orientations (e.g., multiple planes or features on different sides), multiple setups or fixtures may be necessary to complete the job.
- Tool reach and access: Some features may require different tools with specific lengths, diameters, or geometries, necessitating a sequence of machining operations to access hard-to-reach areas.
- Post-Processing Requirements
- Secondary operations: Some parts may require additional treatments, such as heat treating, coating, or assembly, that could affect the material or dimensions. Machining certain features, post-treatment may be required to achieve final specifications.
- Deburring and polishing: Complex parts often require manual or automated deburring and polishing, which may need to be integrated into the machining sequence as a separate step.
Multi-step processing is ideal when dealing with complex geometries, critical tolerances, challenging materials, or when maximizing quality and precision is vital. Experienced machinists consider these points when developing the best strategies for machining large and complex parts. Multi-step processing allows for greater flexibility, control, and adaptability in the manufacturing process. Contact Nolte Precise Manufacturing to learn how multi-step processing improves efficiency and quality.