Just as NFL football coaches have a game plan prior to a rival match-up, you must similarly plan with your machine shop by assembling a production schedule for your parts manufacturing. Streamlining production schedules between a manufacturer and a machine shop requires coordinated planning, efficient communication, and process alignment.
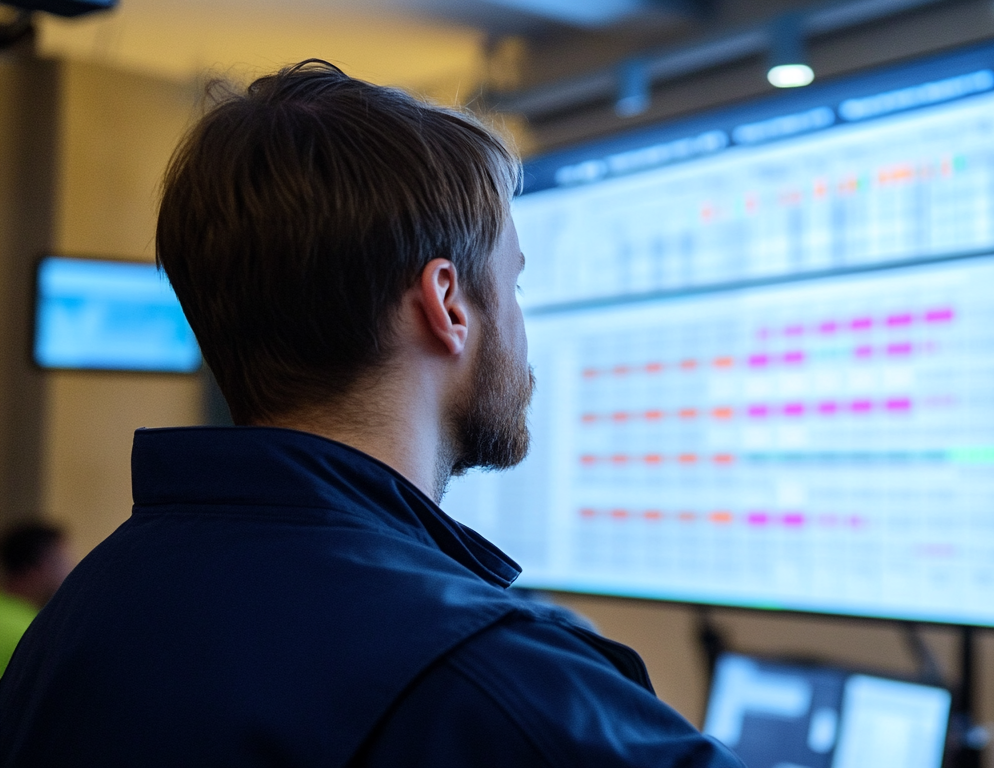
Here are some practical steps both parties can take in streamlining production schedules to improve production efficiency:
- Collaborate on Production Planning
- Shared Forecasting: The manufacturer can provide the machine shop with production forecasts, outlining expected demand for each part. This allows the shop to anticipate workload and optimize scheduling.
- Batch Scheduling: Group similar parts or parts made from the same material into batches to minimize setup times. Scheduling by material or machine type reduces machine changeovers and improves efficiency.
- Optimize Order Quantities and Lead Times
- Order Prioritization: Prioritize critical orders and communicate any changes in demand in real time. This helps avoid rushed jobs and allows the shop to schedule their work more effectively.
- Reduce Setup Times: Work together to determine the ideal lot sizes that balance production costs and time. Minimizing setup times per batch can free up resources for other jobs.
- Standardize Communication Channels
- Digital Communication Tools: Use shared digital platforms for real-time updates on job status, inventory, and production schedules. Tools like ERP systems, shared calendars, or specialized scheduling software can help ensure both sides are on the same page.
- Point of Contact: Designate a point of contact on each side to streamline communication and handle issues quickly, reducing delays due to miscommunication.
- Design for Manufacturability (DFM)
- Early Collaboration in Design: Involve the machine shop during the design phase to identify potential machining challenges and suggest modifications that make parts easier and faster to machine.
- Standardize Features: Encourage the use of standardized hole sizes, threads, and tolerances that align with the machine shop’s equipment capabilities. This can reduce complexity, speed up machining, and decrease rework.
- Implement Just-in-Time (JIT) Practices
- Kanban System: Use a kanban system to signal the need for more parts from the machine shop. This approach aligns production with actual demand, reducing the need for large inventories and freeing up production capacity.
- Inventory Management: The manufacturer can keep some parts as a buffer stock to smooth over any scheduling fluctuations, but overall, aim to reduce idle inventory to lower holding costs and increase efficiency.
- Continuous Feedback and Process Improvement
- Regular Review Meetings: Set up regular meetings between production and the machine shop to review performance, address bottlenecks, and adjust schedules.
- Quality Feedback Loop: Implement a feedback loop for quality control, so issues are quickly addressed and adjustments are made in real time to reduce rework and scrap rates.
Working and communicating closely with your machine shop partner is vital for success. Both parties aim to maximize efficiency, minimize downtime, and ensure the team can achieve success by meeting production targets. By fostering a close partnership and adopting these streamlined processes, both the manufacturer and the machine shop can better manage their schedules, reduce delays, and ultimately meet production goals more consistently.