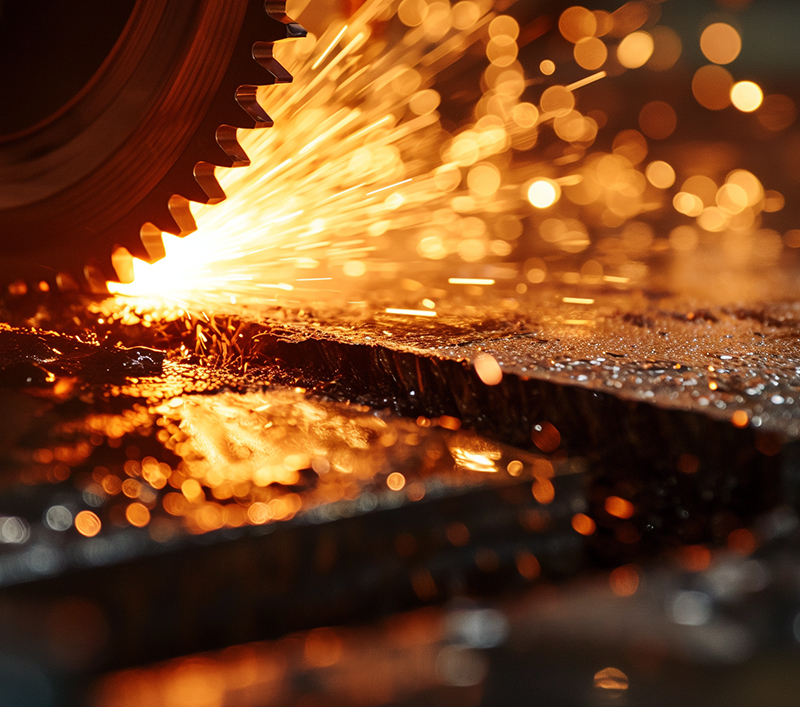
Whether you need precision aerospace, firearms or medical equipment parts, choosing the right part manufacturer, or job shop, who knows the industry can make all the difference in quality, efficiency, and cost-effectiveness. Machine shops offering tailored solutions that meet specific project requirements are the best bet for businesses looking for flexibility, customization, and expert craftsmanship. Partnering with the right job shop can give your business a competitive edge, from specialized expertise to faster turnaround times. So, how does one select the right part manufacturer? There are several key factors to consider that align with production needs, quality standards, and cost considerations.
Top 5 Factors to Set a Job Shop Apart:
- Specialized Capabilities & Expertise – Machine shops often have specialized machinery, processes, and technical expertise manufacturers may not have in-house. This includes CNC machining, laser cutting, precision welding, or other advanced fabrication techniques. The list of machines and machining centers is a great window into the breadth and depth of the types of parts that can be produced.
- Cost Efficiency & Flexibility – Outsourcing your parts can be more cost-effective than maintaining internal production facilities, especially for short-run or custom parts. Job shops offer flexibility in production volumes without requiring significant capital investment.
- Quality & Precision Requirements – Manufacturers choose machine shops with a proven track record of high-quality output, tight tolerances, and adherence to industry standards such as AS9100 for aerospace and defense applications. Maintaining certifications takes time, effort and money. You know that a certified part manufacturer will produce parts in a way that follows industry guidelines and best practices.
- Scalability & Lead Time Reduction – A reliable machine shop helps manufacturers scale production efficiently, whether for prototyping, small batch runs, or full-scale production. Their ability to handle quick turnarounds reduces lead times and improves supply chain responsiveness. Parts manufacturers that work with you closely up front and throughout the production process can help meet your goals.
- Access to Advanced Technology & Innovation – Many job shops invest in cutting-edge technologies such as automation, robotics, additive manufacturing, and AI-driven quality control, providing manufacturers access to innovations they might not have internally. Many strict regulations in the aerospace, medical equipment and defense industries rely on the latest technology to produce parts to spec. The machine shop you select should know the most up-to-date practices to meet your needs.
Partnering with a job shop for your metal parts manufacturing just makes sense. You get the flexibility to handle custom and multiple order sizes, access to skilled machinists who know their craft inside and out, and a team that actually listens to your needs. Plus, machine shops often move faster and adapt to changes better without getting bogged down by mass production. If you’re looking for a reliable, cost-effective way to get high-quality metal parts without the headaches, consider a machine shop for your next project.